HDPE
PE (Polyethylene) Pipe
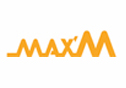
PE Pipes are one of the two largest thermoplastic pipelines available and by far the most versatile. Polyethylene is a wax like thermoplastic with a density varying from a range of 934 Kg/m3 to 960 Kg/m3 which is less than that of water. The only two additives that are added to polyethylene are Carbon black with a limit of 2-3% to add some reinforcing effect to increase its weathering properties and some Anti-Oxidant to a limit of 0.3%. We mostly use black pre-compounded PE material. HDPE having comparatively high molecular weight is high in abrasion resistance and impact strength. It is also very good in stress cracking resistance and has low creep rupture properties. It is excellent in insulation properties over a wide range of frequencies and good chemical properties.
State-of-the-adt HDPE Pipe plant at Silvassa
Ultra modern manufacturing unit
Raw Material
PE Pipes are manufactured from virgin raw material. The wide varieties of materials such as PE-63, PE-80 and PE-100 have varied MRS (Minimum Required Strength) values. Both excellent weathering ability and resistance to UV light can be obtained by utilizing the correct material configuration available in the market.
Applications
The company is equipped with most modern automatic extrusion lines for making pipes ranging from 20 mm OD to 1400 mm OD of pressure range PN 2.5 to PN 16. PE Pipes can act as an ideal substitute for Galvanised iron, Cast iron and other material pipes — appropriate for varied applications such as Potable Water Services or Distribution lines, Sewerage & Drainage, Electrical Ducting, Natural Gas distribution, Irrigation, Waste Disposal, Industrial & Mining applications, Offshore pipeline installations under different climatic conditions as also or transportation of major aggressive chemicals.
Fabricated Fittings
Time Technoplast also fabricates PE fittings to suit specific applications, thus providing a complete solution to all customer requirements. Accessories like bends, tees, flanges, slint.
Quality and Testing Facilities
PE Pipes are made with quality assurance system and strict adherence to IS : 4984, IS : 14333, IS : 14151, ISO : 4427, ASTM D 2239, D 2447, D 3035, F 714, AS AE – 435, AS – 2698.1, BS – 6437, DIN 8074/5 design and testing code to match the quality of our products and services.
Quality Control & Testing Laboratory
PE Pipes Jointing methods
PE pipes can be joined by different means depending upon end use requirements. Some of the jointing techniques are as follows.
For permanent joints
- Butt Fusion Welding joint (widely used)
- Socket Fusion joint
- Electro Fusion joint
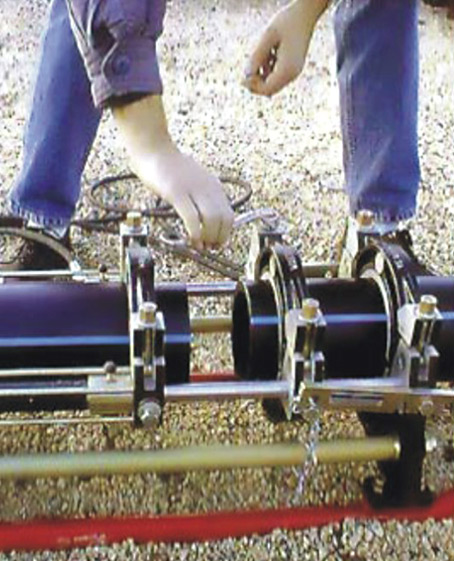
Butt Fusion Welding joint
- Clean both ends with a damp cloth to dislodge any foreign matter or dirt deposited on the pipe.
- Hold the pipes firmly with the clamps of a specially designed welding jack.
- Bring both the faces to axial alignment by using support rollers to minimize mismatch of the faces by rotating, if necessary.
- Carefully remove the oxidized layer on the butts by using a scrapper or a planner.
- Bring both faces in contact with an electrically heated welding mirror maintained at temperature of 210 ± 5°C. Fuse the butts by applying a slight pressure of around 0.2 kg/cm. The pipe material melts and forms a uniform circular rim on the periphery of both the pipe faces.
- Remove the heating mirror and quickly bring both ends in contact with enough pressure.
- Allow the joint to cool to ambient temperature under pressure.
- Open the clamps and remove the pipes from the welding jack.
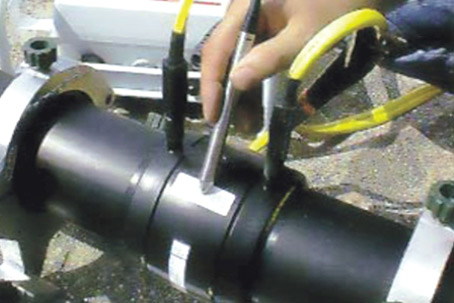
Socket Fusion joint
- For smaller diameter PE pipes, socket heat fusion technique is adopted.
- In this technique individual pipe lengths are joined by heat fusing the outside surface of the pipe to the inside surface of fitting.
- It is mainly used for industrial & domestic plumbing systems.
- For this purpose a special equipment is available that simultaneously heats these two surfaces to fusion temperature.
Electro Fusion joint
- In this method the socket of the fitting incorporates an electrical heating coil.
- When energized by an electronic control unit, the coil causes the material around it to melt and form an expanding pool which comes in contact with the surface of the pipe. This causes the pipe to melt, leading to fusion of pipes & socket.
- Used for air / gas distribution lines.
For Mobile (detachable) joints
- Compression joint
- Flanged joints
- Quick release joints
- Insert joints